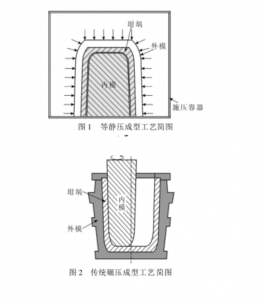
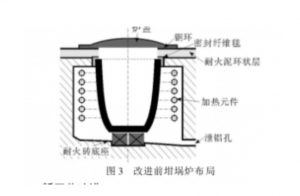
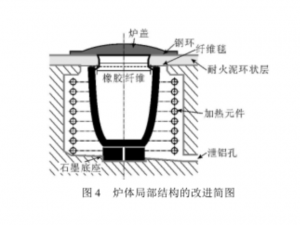
La producción de crisol de grafito ha evolucionado significativamente con el advenimiento de la tecnología de urgencia isostática, marcándola como la técnica más avanzada a nivel mundial. En comparación con los métodos de embrujos tradicionales, la presión isostática da como resultado crisoles con textura uniforme, mayor densidad, eficiencia energética y resistencia superior a la oxidación. La aplicación de alta presión durante el moldeo mejora significativamente la textura del crisol, reduciendo la porosidad y, posteriormente, aumentando la conductividad térmica y la resistencia a la corrosión, como se ilustra en la Figura 1. En un entorno isostático, cada parte de las experiencias de crisol uniformes uniformes de moldeo, lo que garantiza la consistencia del material en todo momento. Este método, como se muestra en la Figura 2, supera el proceso de embrujos tradicional, lo que lleva a una mejora sustancial en el rendimiento crisol.
1. Declaración del problema
Surge una preocupación en el contexto de un horno de crisol de alambre de resistencia de aislamiento de aleación de aluminio utilizando crisoles de grafito embrujados, con una vida útil de aproximadamente 45 días. Después de solo 20 días de uso, se observa una disminución notable de la conductividad térmica, acompañada de microgrietas en la superficie exterior del crisol. En las etapas posteriores de uso, es evidente una caída severa en la conductividad térmica, lo que hace que el crisol sea casi no conductivo. Además, se desarrollan múltiples grietas superficiales y se produce decoloración en la parte superior del crisol debido a la oxidación.
Al inspeccionar el horno de crisol, como se muestra en la Figura 3, se utiliza una base compuesta de ladrillos refractarios apilados, con el elemento de calentamiento de Bottommost del cable de resistencia situado a 100 mm sobre la base. La parte superior del crisol está sellada con mantas de fibra de asbesto, colocadas a unos 50 mm del borde exterior, revelando una abrasión significativa en el borde interno de la parte superior del crisol.
2. Nuevas mejoras tecnológicas
Mejora 1: Adopción del crisol de grafito de arcilla prensado isostático (con glaseado resistente a la oxidación a baja temperatura)
La utilización de este crisol mejora significativamente su aplicación en los hornos de aislamiento de aleación de aluminio, particularmente en términos de resistencia a la oxidación. Los crisoles de grafito típicamente se oxidan a temperaturas superiores a 400 ℃, mientras que la temperatura de aislamiento de los hornos de aleación de aluminio oscila entre 650 y 700 ℃. Los crisoles con glaseado resistente a la oxidación a baja temperatura pueden ralentizar efectivamente el proceso de oxidación a temperaturas superiores a 600 ℃, lo que garantiza una excelente conductividad térmica prolongada. Simultáneamente, evita la reducción de la resistencia debido a la oxidación, extendiendo la vida útil del crisol.
Mejora 2: base de horno que utiliza el grafito del mismo material que el crisol
Como se muestra en la Figura 4, el uso de una base de grafito del mismo material que el crisol garantiza el calentamiento uniforme del fondo del crisol durante el proceso de calentamiento. Esto mitiga los gradientes de temperatura causados por el calentamiento desigual y reduce la tendencia de las grietas resultantes del calentamiento inferior desigual. La base de grafito dedicada también garantiza un soporte estable para el crisol, alineándose con su trasero y minimizando las fracturas inducidas por el estrés.
Mejora 3: Mejoras estructurales locales del horno (Figura 4)
- El borde interno mejorado de la cubierta del horno, evitando efectivamente el desgaste en la parte superior del crisol y que mejora significativamente el sellado del horno.
- Asegurar que el cable de resistencia esté nivelado con el fondo del crisol, garantizando suficiente calentamiento de fondo.
- Minimizar el impacto de los sellos de la manta de fibra superior en el calentamiento de crisol, asegurando el calentamiento adecuado en la parte superior del crisol y reduciendo los efectos de la oxidación a baja temperatura.
Mejora 4: Refinamiento de procesos de uso de crisol
Antes del uso, precaliente el crisol en el horno a temperaturas inferiores a 200 ℃ durante 1-2 horas para eliminar la humedad. Después de precalentar, eleve rápidamente la temperatura a 850-900 ℃, minimizando el tiempo de permanencia entre 300-600 ℃ para reducir la oxidación dentro de este rango de temperatura. Posteriormente, reduzca la temperatura a la temperatura de trabajo e introduzca material líquido de aluminio para el funcionamiento normal.
Debido a los efectos corrosivos de los agentes de refinación en los crisoles, siga los protocolos de uso correctos. La eliminación regular de la escoria es esencial y debe realizarse cuando el crisol está caliente, ya que la escoria de limpieza se vuelve desafiante de otra manera. La observación vigilante de la conductividad térmica del crisol y la presencia de envejecimiento en las paredes de crisol es crucial en las etapas posteriores de uso. Se deben hacer reemplazos oportunos para evitar la pérdida innecesaria de energía y la fuga de líquido de aluminio.
3. Resultados de mejora
La vida útil extendida del crisol mejorado es notable, manteniendo la conductividad térmica para duraciones prolongadas, sin que se observara grietas superficiales. La retroalimentación del usuario indica un rendimiento mejorado, no solo reduce los costos de producción, sino que también mejora significativamente la eficiencia de producción.
4. Conclusión
- Los cruzados de grafito de arcilla prensados isostáticos superan a los crisoles tradicionales en términos de rendimiento.
- La estructura del horno debe coincidir con el tamaño y la estructura del crisol para un rendimiento óptimo.
- El uso adecuado del crisol extiende significativamente su vida útil, controlando efectivamente los costos de producción.
A través de una investigación meticulosa y la optimización de la tecnología de hornos de crisol, el rendimiento mejorado y la vida útil contribuyen sustancialmente a una mayor eficiencia de producción y ahorros de costos.
Tiempo de publicación: Dic 24-2023