Cobre (Cu)
Cuando el cobre (Cu) se disuelve en aleaciones de aluminio, las propiedades mecánicas mejoran y el rendimiento de corte mejora. Sin embargo, la resistencia a la corrosión disminuye y el agrietamiento en caliente es propenso a ocurrir. El cobre (Cu) como impureza tiene el mismo efecto.
La resistencia y la dureza de la aleación puede aumentarse significativamente con el contenido de cobre (Cu) superior a 1.25%. Sin embargo, la precipitación de Al-Cu provoca la contracción durante la fundición a la matriz, seguida de la expansión, lo que hace que el tamaño del fundido sea inestable.
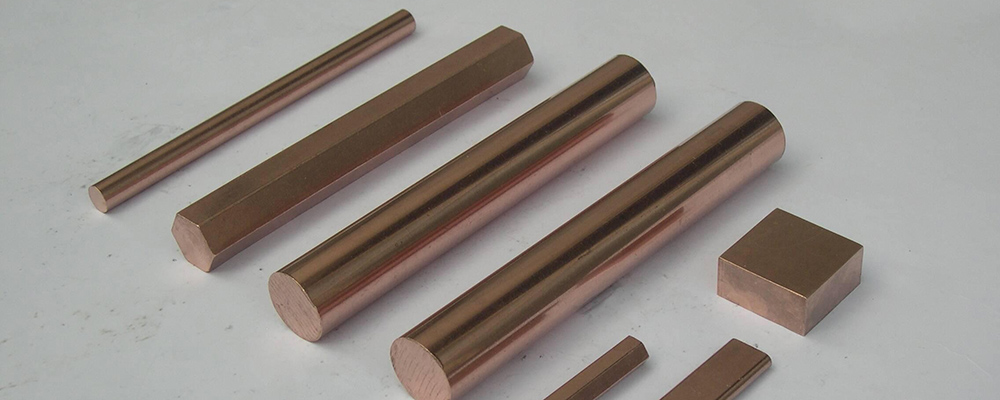
Magnesio (mg)
Se agrega una pequeña cantidad de magnesio (mg) para suprimir la corrosión intergranular. Cuando el contenido de magnesio (mg) excede el valor especificado, la fluidez se deteriora y la fragilidad térmica y la resistencia al impacto se reducen.
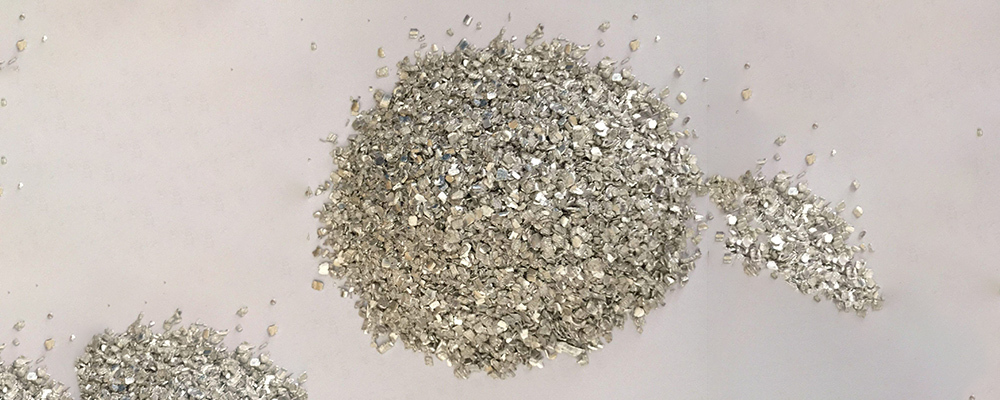
Silicio (Si)
El silicio (SI) es el ingrediente principal para mejorar la fluidez. La mejor fluidez se puede lograr de eutéctica a hipereutéctica. Sin embargo, el silicio (SI) que cristaliza tiende a formar puntos difíciles, lo que empeora el rendimiento de corte. Por lo tanto, generalmente no está permitido exceder el punto eutéctico. Además, el silicio (SI) puede mejorar la resistencia a la tracción, la dureza, el rendimiento de corte y la fuerza a altas temperaturas al tiempo que reduce el alargamiento.
La aleación de magnesio de magnesio (mg) tiene la mejor resistencia a la corrosión. Por lo tanto, ADC5 y ADC6 son aleaciones resistentes a la corrosión. Su rango de solidificación es muy grande, por lo que tiene la fragilidad caliente, y los moldes son propensos a agrietarse, lo que dificulta el lanzamiento. El magnesio (mg) como impureza en los materiales al-CU-Si, MG2SI hará que la fundición sea frágil, por lo que el estándar generalmente está dentro del 0.3%.
Hierro (Fe) Aunque el hierro (Fe) puede aumentar significativamente la temperatura de recristalización del zinc (Zn) y ralentizar el proceso de recristalización, en la fusión de fundición a muerte, el hierro (Fe) proviene de crisoles de hierro, tubos de cuello de cementera y herramientas de fusión, y es soluble en zinc (Zn). El hierro (Fe) transportado por aluminio (Al) es extremadamente pequeño, y cuando el hierro (Fe) excede el límite de solubilidad, se cristalizará como Feal3. Los defectos causados por Fe generan escoria y flotación como compuestos Feal3. El casting se vuelve frágil y la maquinabilidad se deteriora. La fluidez del hierro afecta la suavidad de la superficie de fundición.
Las impurezas de hierro (Fe) generarán cristales de Feal3 en forma de aguja. Dado que la fundición a muerte se enfría rápidamente, los cristales precipitados son muy finos y no pueden considerarse componentes dañinos. Si el contenido es inferior al 0.7%, no es fácil de desmoldarse, por lo que el contenido de hierro de 0.8-1.0% es mejor para la fundición a muerte. Si hay una gran cantidad de hierro (Fe), se formarán compuestos de metal, formando puntos difíciles. Además, cuando el contenido de hierro (Fe) excede el 1,2%, reducirá la fluidez de la aleación, dañará la calidad de la fundición y acortará la vida de los componentes de metal en el equipo de fundición a muerte.
Níquel (Ni) como el cobre (Cu), hay una tendencia a aumentar la resistencia y la dureza de la tracción, y tiene un impacto significativo en la resistencia a la corrosión. A veces, se agrega níquel (Ni) para mejorar la resistencia a la alta temperatura y la resistencia al calor, pero tiene un impacto negativo en la resistencia a la corrosión y la conductividad térmica.
Manganeso (MN) puede mejorar la resistencia a la alta temperatura de las aleaciones que contienen cobre (Cu) y silicio (SI). Si excede un cierto límite, es fácil generar compuestos cuaternarios al-Si-Fe-P+O {t*t f; x mn, que pueden formar fácilmente puntos duros y reducir la conductividad térmica. El manganeso (MN) puede evitar el proceso de recristalización de las aleaciones de aluminio, aumentar la temperatura de recristalización y refinar significativamente el grano de recristalización. El refinamiento de los granos de recristalización se debe principalmente al efecto obstaculizado de las partículas compuestas MNAL6 en el crecimiento de los granos de recristalización. Otra función de MNAL6 es disolver la impureza de hierro (Fe) para formar (Fe, Mn) AL6 y reducir los efectos nocivos del hierro. El manganeso (MN) es un elemento importante de las aleaciones de aluminio y se puede agregar como una aleación binaria Al-MN independiente o junto con otros elementos de aleación. Por lo tanto, la mayoría de las aleaciones de aluminio contienen manganeso (MN).
Zinc (Zn)
Si el zinc impuro (Zn) está presente, exhibirá la fragilidad de alta temperatura. Sin embargo, cuando se combina con mercurio (Hg) para formar aleaciones fuertes de HGZN2, produce un efecto de fortalecimiento significativo. JIS estipula que el contenido de zinc impuro (Zn) debe ser inferior al 1.0%, mientras que los estándares extranjeros pueden permitir hasta el 3%. Esta discusión no se refiere al zinc (Zn) como un componente de aleación, sino que su papel como impureza que tiende a causar grietas en las piezas de fundición.
Cromo (CR)
El cromo (Cr) forma compuestos intermetálicos como (CRFE) AL7 y (CRMN) AL12 en aluminio, obstaculizando la nucleación y el crecimiento de la recristalización y proporcionando algunos efectos de fortalecimiento a la aleación. También puede mejorar la dureza de la aleación y reducir la sensibilidad a la corrosión de estrés. Sin embargo, puede aumentar la sensibilidad de enfriamiento.
Titanio (TI)
Incluso una pequeña cantidad de titanio (Ti) en la aleación puede mejorar sus propiedades mecánicas, pero también puede disminuir su conductividad eléctrica. El contenido crítico del titanio (TI) en las aleaciones de la serie Al-TI para el endurecimiento por precipitación es de aproximadamente 0.15%, y su presencia puede reducirse con la adición de boro.
Lead (PB), TIN (SN) y Cadmium (CD)
El calcio (CA), el plomo (Pb), la lata (Sn) y otras impurezas pueden existir en las aleaciones de aluminio. Dado que estos elementos tienen diferentes puntos y estructuras de fusión, forman diferentes compuestos con aluminio (AL), lo que resulta en diferentes efectos en las propiedades de las aleaciones de aluminio. El calcio (CA) tiene una solubilidad sólida muy baja en el aluminio y forma compuestos Caal4 con aluminio (AL), lo que puede mejorar el rendimiento de corte de las aleaciones de aluminio. El plomo (Pb) y la estaño (SN) son metales de bajo punto de fusión con baja solubilidad sólida en aluminio (AL), lo que puede reducir la resistencia de la aleación pero mejorar su rendimiento de corte.
Aumentar el contenido de plomo (Pb) puede reducir la dureza del zinc (Zn) y aumentar su solubilidad. Sin embargo, si alguno de plomo (Pb), estaño (Sn) o cadmio (CD) excede la cantidad especificada en un aluminio: aleación de zinc, puede ocurrir corrosión. Esta corrosión es irregular, ocurre después de un cierto período y es particularmente pronunciada bajo atmósferas de alta temperatura y alta humedad.
Tiempo de publicación: mar-09-2023